ACE was approached by a major iron ore miner to improve the life of their middlings chute ledge liners. The liners would routinely require changeout every 32 weeks. ACE proposed changing the wear block from a Ni-hard casting to a CMZ wear billet. For the purposes of the trial, every second billet was changed to CMZ, in order to get a side-by-side comparison of the wear characteristics of the liners. It was understood that the CMZ billet will potentially slow the overall wear rate of the neighbouring Ni-Hard billet, and this was taken into account.
ACEblokCMZ Case Study
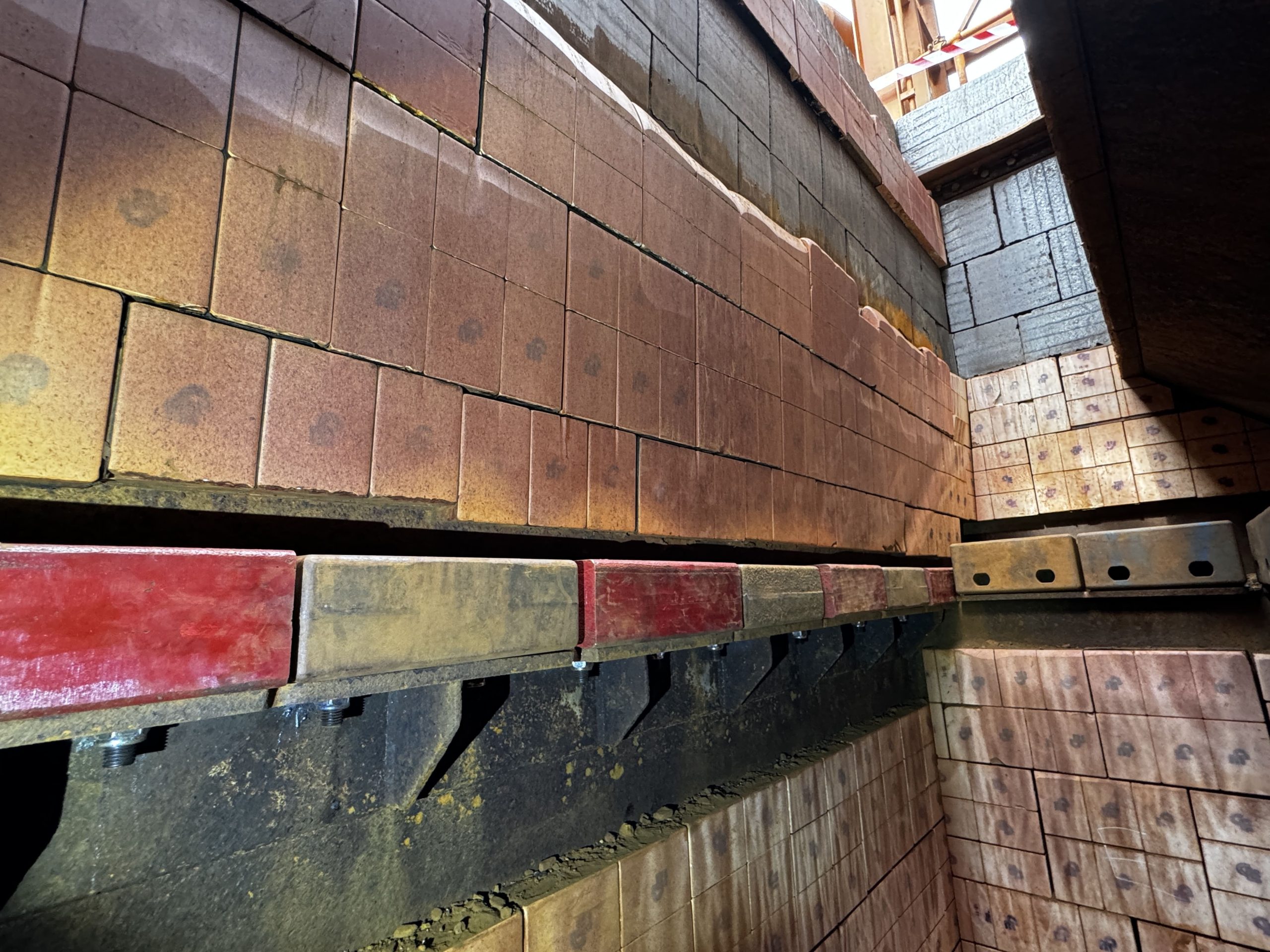
ACEblokCMZ wear billets consist of a ZTA ceramic insert cast into the toe of a 15-3 Cr-Mo white iron wear block. The resulting material combines the impact resistance of a 15-3 Cr-Mo white iron casting
with the extreme wear resistance of the ZTA ceramic. The advantage of this wear billet includes significantly longer wear life, high impact resistance and is available in all standard and custom configurations. The improvement in wear and impact performance results in a lower cost per tonne of ore mined and a reduction in down time and maintenance costs.
The middlings chute was inspected every 16 weeks after the instillation of the CMZ billets, and the resulting reported wear were as follows:
NI-HARD 4 LINERS
Week 16: 50% wear on all ledge billets. No liners replaced.
Week 35: 90% wear on all liners. All liners replaced alternating between Ni-Hard 4 and CMZ.
CMZ TRIAL INSTALL 50-50
Week 16: Average wear of 20%, with some liners worn up to 40%, with most wear at the interface between liners.
Week 32: Average wear reported at 50%, all billets changed to CMZ
ALL LINERS CMZ
Week 16: Average wear reported at 15%, no action taken.
Week 32: Average wear reported between 30 and 40%, no action taken.
Week 48: Average wear reported at 50%, no action taken.
Further monitoring of the trial install is required to determine the overall increase in wear life, however the initial data reported is showing a major increase in wear performance over standard Ni-Hard 4 wear material. The frequent need for shutdowns posed a significant safety and environmental risk, including exposure to confined spaces and hot work conditions. The additional cost of the wear liner is mitigated by the reduction in shut requirements due to the additional wear life as well as the health and safety issues related to shut down work.
Contact
Address
Sales Enquiries
Carl Van Tonder +61 457 828 805
Shane Arnold +61 410 645 449
Site Services
Gab Mikhail 08 9303 9944